HCX
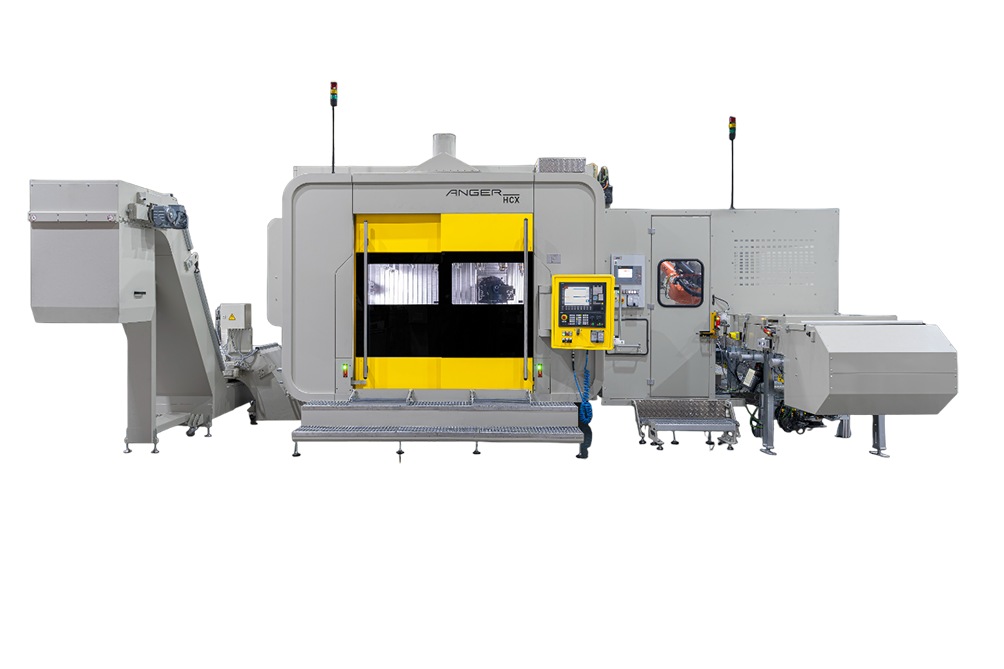
The ANGER HCX Turn Key systems are specifically designed to meet the needs of the customers. The plant is designed, constructed and automated according to the specific parts. As a result, the highly productive HCX systems achieve the shortest cycle times with the highest accuracy. These are highly productive plants with maximum output rates.
Depending on the complexity of the workpiece, an ANGER HCX machine achieves a cycle time and output quantity of at least two double-spindle BAZ. Compared to single spindle BAZ, one HCX replaces at least 4, in some cases even up to 8 machining centers.
Technical Details
Number of axis | 4 |
Spindles | 2 |
Downloads

YOUR ADVANTAGES
- Minimum cycle times guarantee maximum production output
- Lowest TCO costs reduce your manufacturing costs
- Highest accuracies guarantee high component quality
- Longer spindle service life through optimized processes

The most qualitative manufacturing
- Customized specification booklet filling
- Individual layout
- Automation and integration into your production halls
- Design of special machines
You have questions about our machines?
We will be happy to advise you and develop an individual solution together with you.
Frequently asked questions
How many parts can be machined in parallel?Depending on the component geometry and customer requirements, up to 3 components can be processed in parallel in the transfer center.
What is meant by envelope errors in machining?The wrap error occurs with opposing holes that require the part to be rotated 180° to produce them. This problem can be circumvented by fixed machining spindles arranged opposite each other.
What is a multi-spindle head?A multi-spindle head is a machining unit that contains several machining spindles and tools. This makes it possible to carry out several processing steps such as e.g. To perform cutting of threads in one stroke. This enables very high machine outputs with maximum efficiency.
What is a transfer center?A transfer center is a CNC machining center where, unlike conventional centers, a workpiece is fed through a series of fixed machining spindles. Since tool change times are completely eliminated, the highest output rates and the tightest machining tolerances are possible.

Customer support